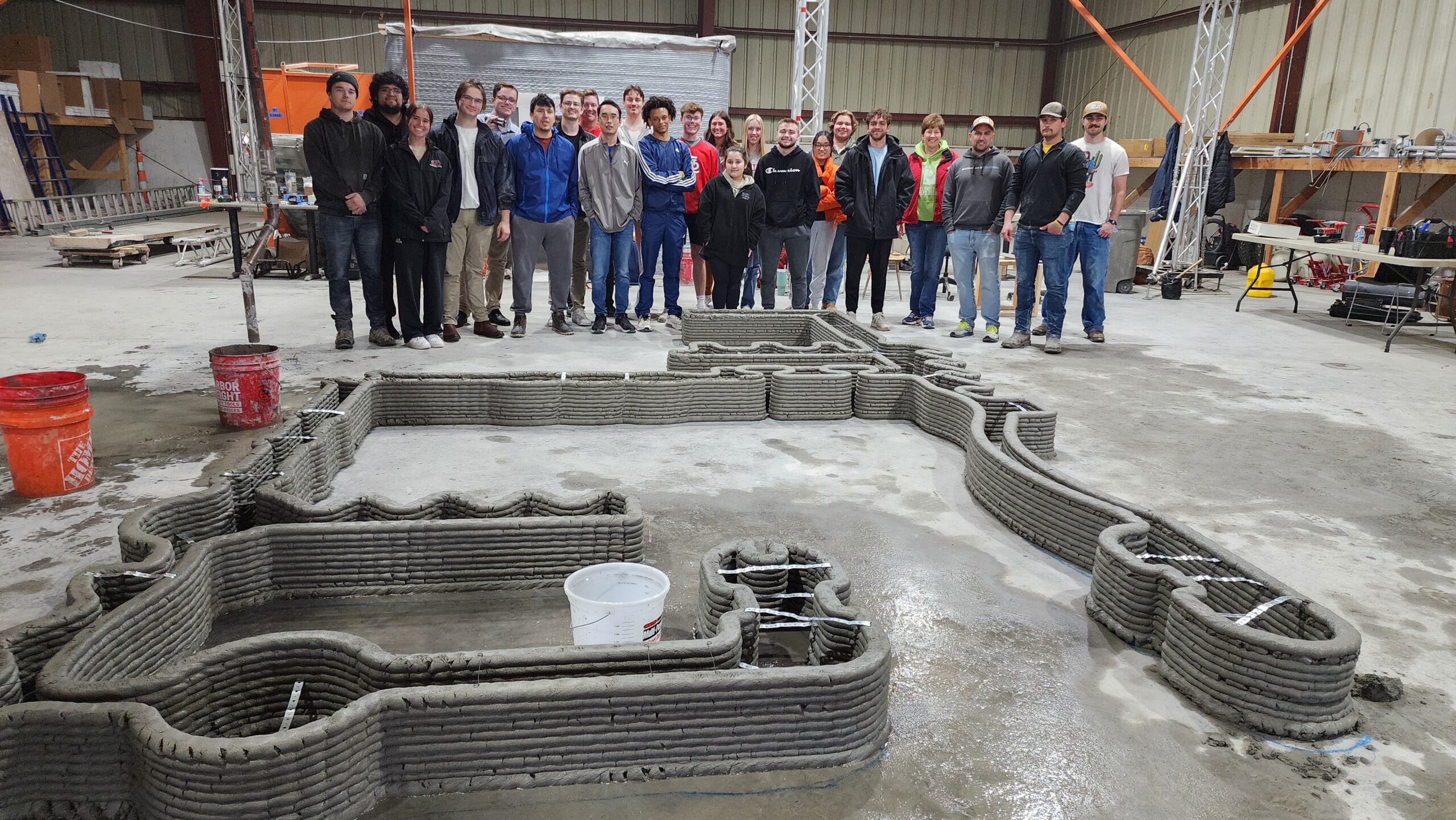
How concrete 3D printing is shaping the future of affordable housing and architectural innovation
Campus March 5, 2025, Comments Off 109In 2024, the first full scale 800 square feet duplex was successfully built using the concrete 3D printing technology in Lamar, Missouri. Six days was the total amount of time for a complete wall system and structure to be printed, layer by layer. The roof and foundation of the duplex were constructed with conventional methods.
The design and construction of the duplex was led by Traci Sooter, a professor at the Hammons School of Architecture at Drury University, and other members of The Gathering Tree. Professor Sooter has also begun teaching this technology through studio courses since 2023.
The journey to explore 3D printing with concrete provides the Gathering Tree’s construction team and Drury students practical learning experience with the machine and working with concrete. Since Covid-19, construction prices have doubled and halted the Eden Village III project, led by The Gathering Tree, that provides supportive housing for the disabled unhoused people.
According to professor Sooter, prices for each tiny house was $35,000 before Covid-19 and increased up to $67,000. Nate Schlueter, the CEO of The Gathering Tree, identified Concrete 3D Printing to be a viable solution that could bring down the costs.
After the purchase of two printers from Utah, CEO Schlueter and his crew have made many adjustments to the machines to improve their tools and functionality. Currently, a printer is located at Drury University for student research and their experiments.
Drury’s Beth Harville, the Senior Executive Vice President Provost and Alex Riddle, the Executive Director of Facilities, provided tremendous help in preparing the warehouse space to store the 33’ by 55’ 3D printer on campus. The other one is the traveling printer with the Gathering Tree for on-site construction.
According to Professor Sooter, the most challenging aspect when 3D printing with concrete is the consistency of the concrete mixture being affected by the outdoor environment. With the variables in wind, sun, temperature, and humidity, the printing process can either speed up or slow down. The Gathering Tree team spent 5 weeks training in Utah to learn about the printing process.
“You’re printing a layer 1 ½ inch wide and ¾ of an inch thick,” Professor Sooter shares. “Then layering on top of that straight up a few feet. Your mix must be perfect; it cannot be too wet or too dry”.
After several tests, the Gathering Tree construction team has also learned to use Southwest Missouri Portland cement and water with different minerals which could affect the print result. According to Professor Sooter, “The key here is to develop relationships with these folks who donate the materials so that our Portland cement and sand have the same minerals and give us the consistency we need.” While the 3D printing technology has not yet been perfected, Drury University is on the leading edge that helps move the technology forward.
In studio courses, students get to experiment with the nozzle designs, concrete textures, printing oscillation, air-release devices, and design forms. With the most current studio course, the fourth-year architecture students initiated a design-build project of a bus stop that also has a built-in community refrigerator.
“We welcome and encourage any student who is interested in the research of this technology to join. It is a highly relevant for essentially everyone who occupies the built environment”. Professor Sooter comments. “Students have really helped us in taking advantage of the 3D printer and using it in an innovative way so that we finally printed our first full-scale duplex in Lamar for the donor of the two 3D printers. In the future, construction time with a project of the same scale will take 2-3 days to print.”
With the ongoing research at Drury University, Professor Sooter anticipated that construction costs could reduce to one third of the current market costs. Students’ research and work will be applied in the Eden Village III project with 12 different duplexes. Each of them will be printed with different oscillation patterns and nozzles that students worked on.
Since the introduction of courses with the concrete 3D printer, some students have had opportunities to further develop their career along with the new technology. Austin Morris, a fifth-year architecture student interned with Eden Building Solution LLC and worked on a full-scale concrete 3D printing project.
“It was a great opportunity to not only design a project but also to gain experience with a leading-edge technology during my internship.” says Morris. “It was incredibly rewarding to see that my work has a positive impact on the community”
Professor Sooter and many students believe that, with further research and development, concrete 3D printing has the potential to address the urgent need for housing and provide shelter for those experiencing homelessness.
Featured photo by Professor Sooter